Department: Pipefitting
It was critical for Lee Contracting’s crew to carefully maneuver the large machinery to the center of the facility, as the plant was still in operation during the installation. Oftentimes, extrusion lines can be too large to transport through an entire facility.
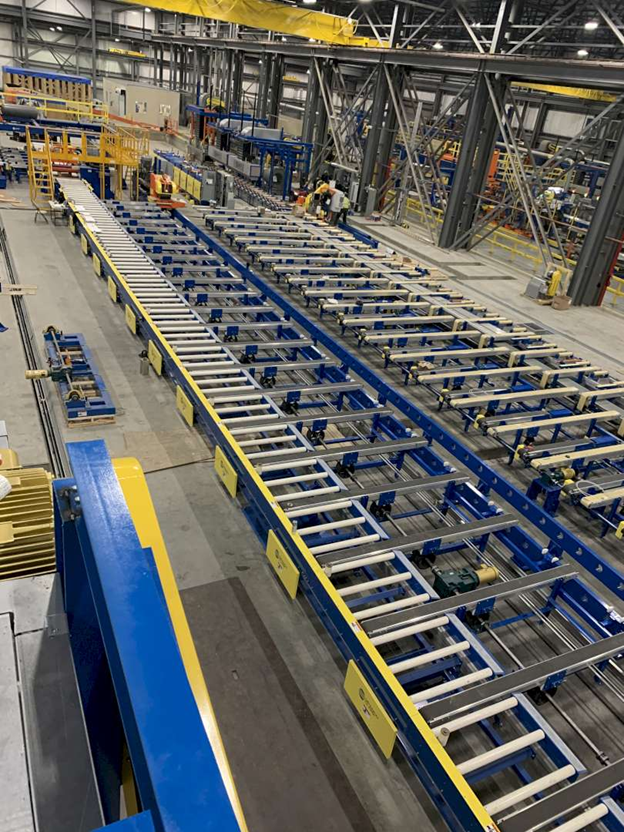
THE CHALLENGE
Granco Clark, a global leader in the aluminum extrusion industry, turned to Lee Industrial Contracting to install an extrusion line for one of their customers.
It was critical for Lee Contracting’s crew to carefully maneuver the large machinery to the center of the facility, as the plant was still in operation during the installation. Oftentimes, extrusion lines can be too large to transport through an entire facility.
THE RESULTS
The Lee Contracting team began with the removal of the old machinery, then they prepped the space for the new line.
Lee Contracting’s solution to prevent transporting the line throughout the facility was to create cutouts in the side of the building. The crew was then able to successfully transport the machinery to its new home, with little interruption. Because the plant was in full production during the entire process, Lee Contracting’s team had to remain flexible and coordinated their work with the production schedule, working nights and weekends as needed.
After the new equipment was brought in, Lee Contracting’s expert team worked around the clock to connect the electrical and main utilities to the machinery.
Since this first project, Granco Clark has turned to Lee to install several extrusion lines and presses for their customers at various locations.
Subscribe and receive updates via email
With winter approaching, and a timeline of less than five months to complete the installation, the challenge was formidable.
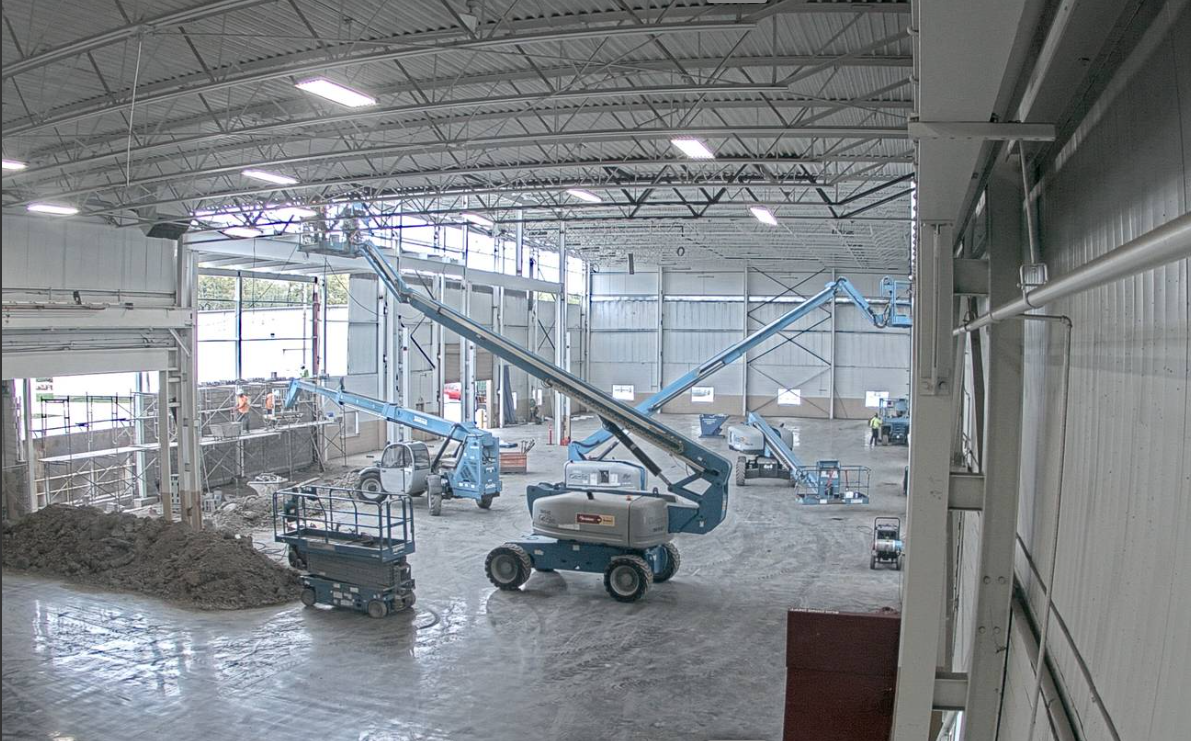
THE CHALLENGE
Wico Metal Products, a pioneer in automotive extrusion stampings, had recently acquired a new facility to set up several new stamping press lines. However, upon acquisition, it became apparent the building’s roof was not high enough to accommodate the 26-foot-tall presses. With winter approaching, and a timeline of less than five months to complete the installation, the challenge was formidable. An additional 12 feet of vertical space was needed. Wico Metal Products reached out to Lee Industrial Contracting for a solution that involved incorporating several in-house trades.
Initial discussions with Wico defined the project scope: raising the roof, demolishing several existing offices, and enclosing a courtyard to expand manufacturing space. Lee Contracting started a thorough design phase, collaborating closely with Wico to finalize a detailed and actionable project plan. This plan was swiftly turned into a comprehensive drawing package for city permit submissions, including structural, architectural, electrical, and plumbing elements.
THE RESULTS
Lee Industrial Contracting expedited the planning and permit process in collaboration with the City of Warren. Once permits were secured, the project shifted into high gear. Lee Contracting’s team prepared the site by modifying the existing roof structure and ensuring all utilities were safely repositioned for the changes ahead.
Subscribe and receive updates via email
Install 300 feet of new 10" SCH 40 roll-grooved black piping while preparing for additional future expansions.
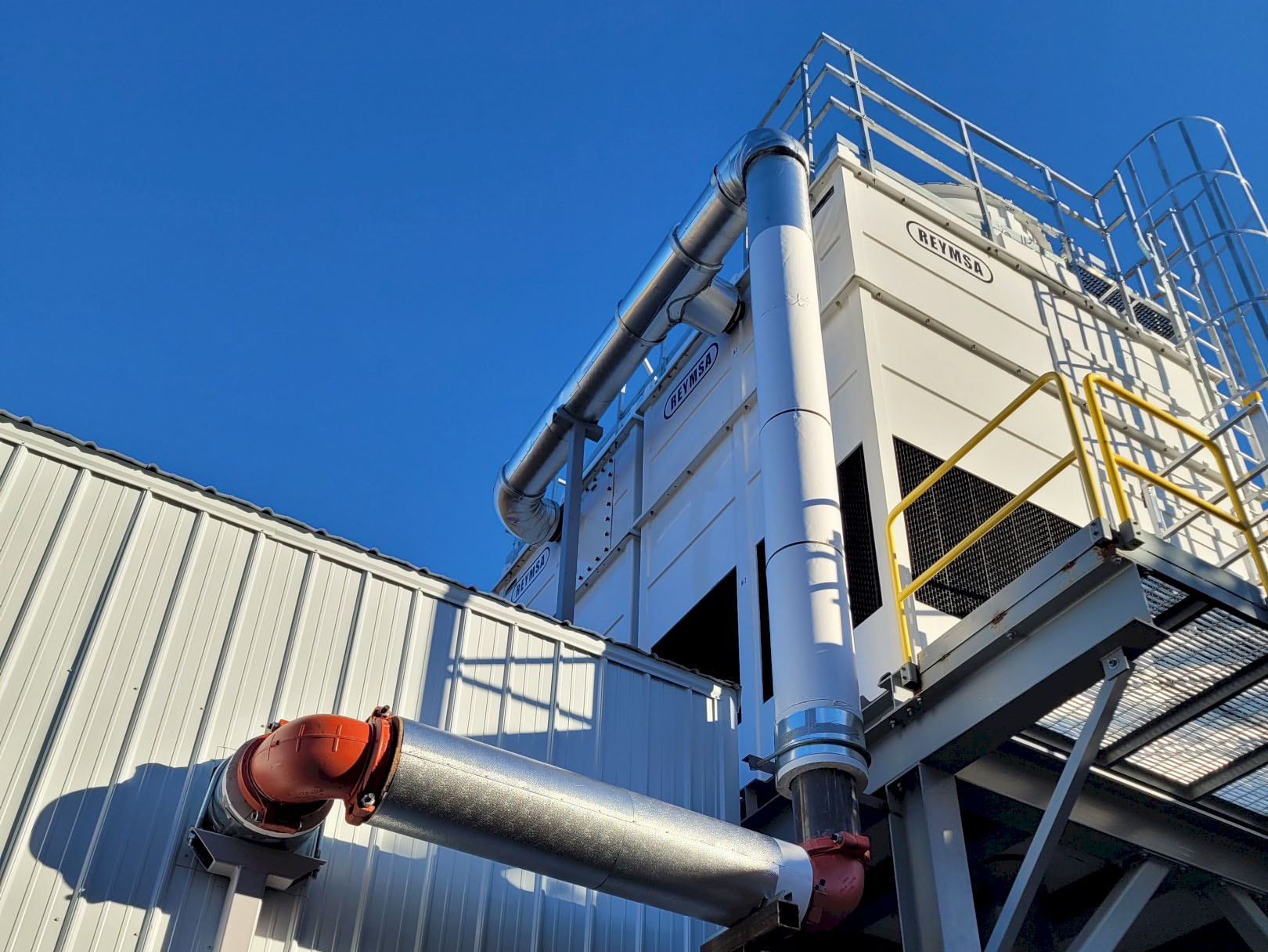
THE CHALLENGE
UTAC, a leading player in the digital and sustainable mobility sector, is known for its customizable testing solutions, systems, vehicle engineering and regulatory expertise. They needed the installation of new piping for a cooling water loop that would be integral to future Dyno cells. The requirement was clear: install 300 feet of new 10″ SCH 40 roll-grooved black piping while preparing for additional future expansions. This task had to be accomplished without disrupting the existing production lines, which posed a logistical challenge.
Lee Industrial Contracting was entrusted with this complex project, which required meticulous planning and execution. The scope of work included insulating the new exterior process water piping with 2″ thick fiberglass insulation and aluminum jacketing. A critical aspect of the project was addressing the significant weight of the new cooling loop system, necessitating structural engineering for joist girder and steel reinforcements, adeptly handled by Lee Contracting’s weld/fab department.
THE RESULTS
In close collaboration with UTAC, Lee Contracting carefully planned the project to ensure zero interruptions to ongoing production. Through their proactive approach and efficient project management, Lee Contracting not only met the requirements but was able to complete the project under budget and two weeks ahead of schedule.
Subscribe and receive updates via email
Repurposing a vacant 40,000-square-foot industrial building, which had previously been used for manufacturing robotic weld cells, into a dynamic sports arena suitable for volleyball, badminton, cricket, and pickleball.
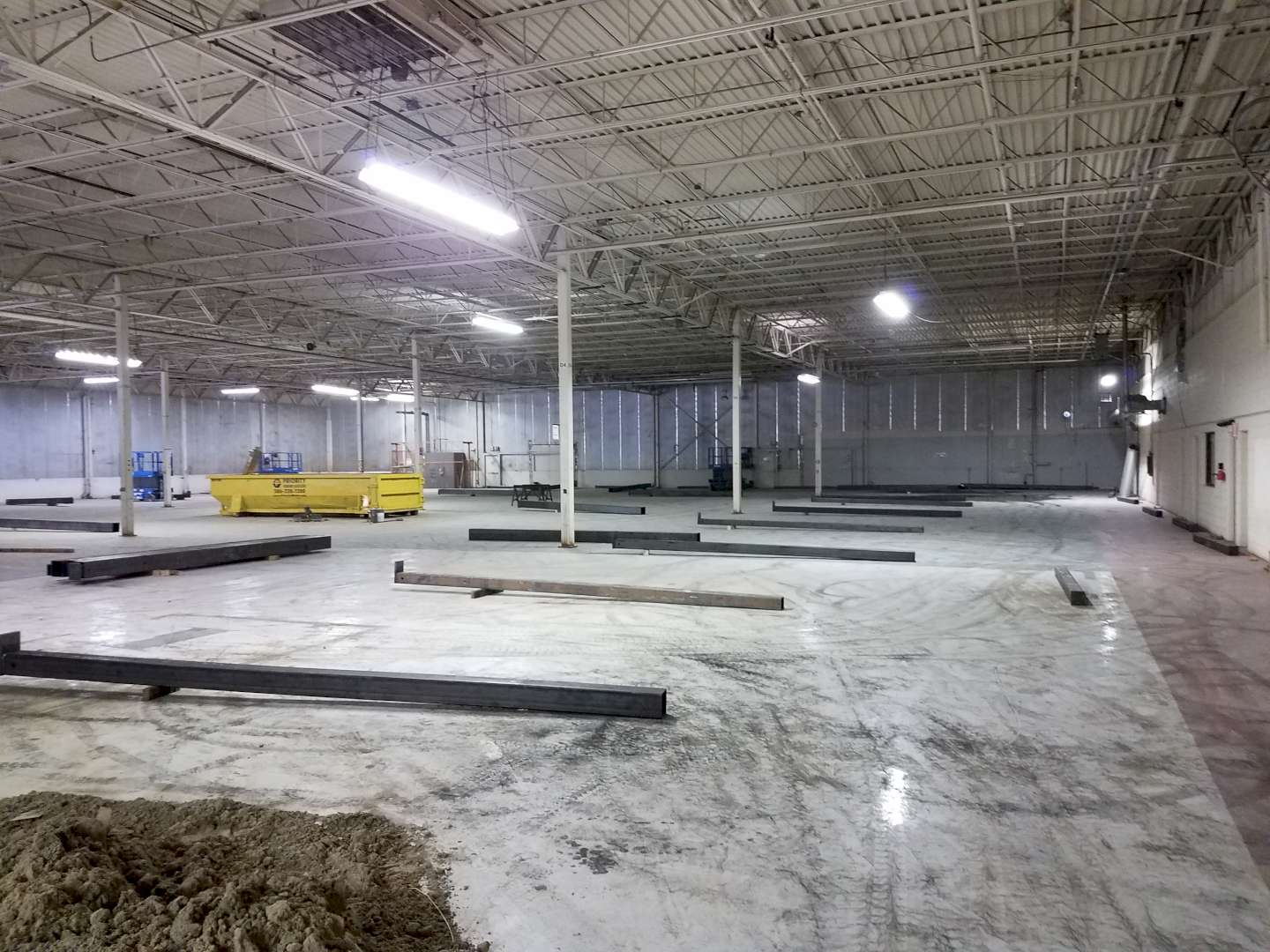
THE CHALLENGE
In the summer of 2020, as the world grappled with the onset of the COVID-19 pandemic, a group of entrepreneurs from Spare Holdings identified an opportunity to create a year-round, indoor sports facility in Novi, Michigan. Their vision was to repurpose a vacant 40,000-square-foot industrial building, which had previously been used for manufacturing robotic weld cells, into a dynamic sports arena suitable for volleyball, badminton, cricket, and pickleball.
The scope of the project included a substantial structural modification-raising a 160′ x 160′ section of the building’s roof by 10 feet. The project involved comprehensive design and construction efforts, encompassing electrical systems, steel structures, HVAC, plumbing, and general building modifications. The principal challenge was executing this intricate project with limited availability of supplies and significant vendor delivery delays. Ensuring safety, managing supply-chain disruptions, and maintaining project timelines under these constraints required careful planning and adaptability.
THE RESULTS
Following a successful planning and permitting phase, including collaboration with the city of Novi and Spare’s team, Lee Contracting initiated the physical transformation of the building in the winter of 2021. The project began with the demolition of existing walls and electrical setups to make room for the new sports courts. Despite facing extended lead times on key materials, such as building siding and rooftop HVAC units stretching from the usual four weeks to over six months Lee Contracting was able to easily navigate these challenges. The team was able to ensure a continuous flow of information and resources to keep the project on track and within budget.
A critical component of the construction was the manufacturing of new structural steel for the roof raise, which included the integration of larger girder beams necessary for the removal of two building columns. This phase culminated in a coordinated five-day process where the roof was elevated in one piece, facilitating the creation of expansive, unobstructed court spaces.
The project not only included structural enhancements but also the installation of new HVAC systems, the construction of modern offices, bathrooms, locker rooms, and a spectator mezzanine. Upon completion of the renovation, Spare awarded a 2nd phase to Lee Contracting that includes raising another 180′ x 80′ section of the building to help their operations meet the growth of their new business.
Subscribe and receive updates via email
The line consisted of two large presses (one 5500T and one 4000T) which required new foundation pits, with some areas having concrete 72" thick, as well as utility trenching with trench covers.
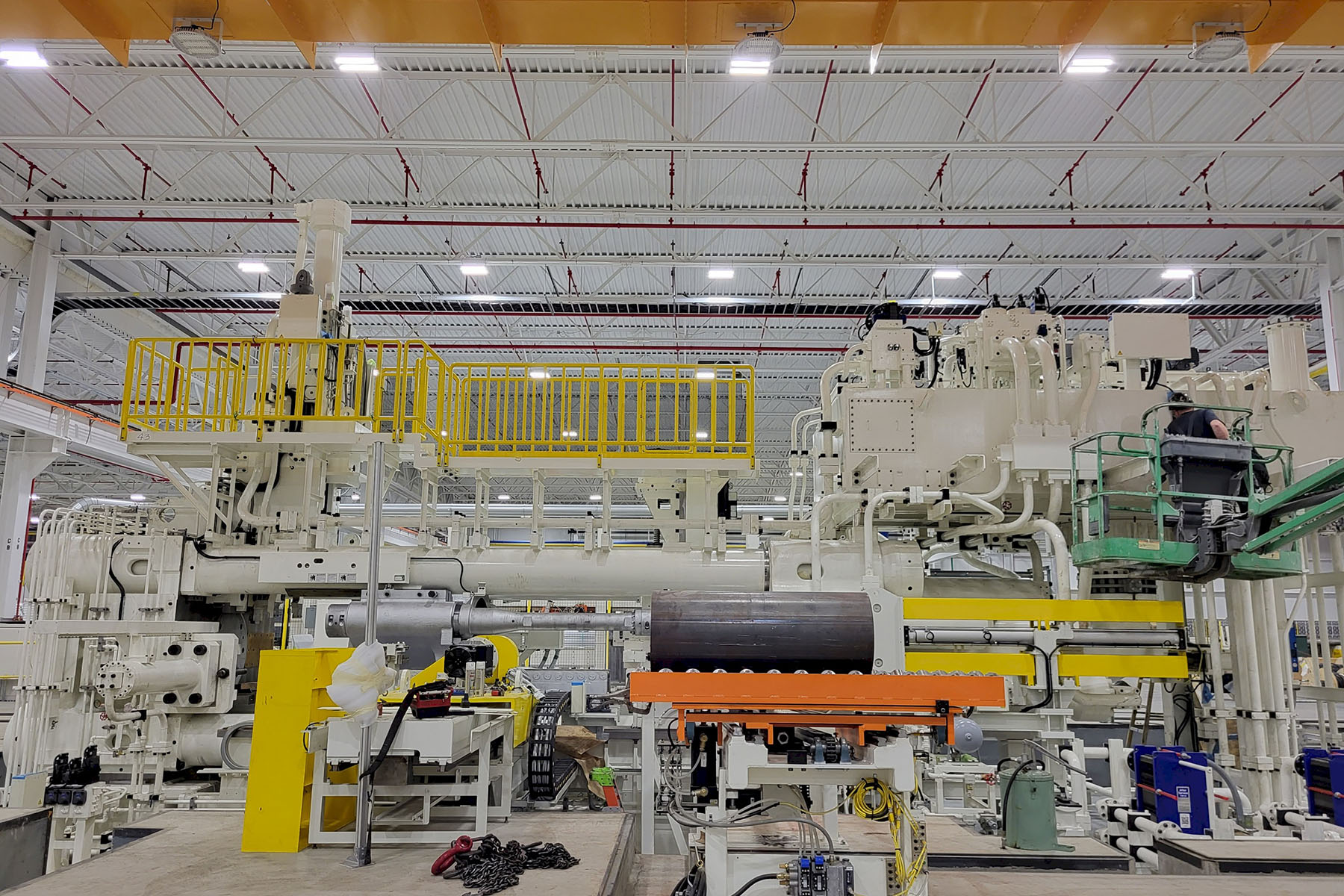
THE CHALLENGE
Shape Corporation needed additional manufacturing capacity within its extrusion facility. The timing and coordination needs of this project made Lee Contracting’s in-house, multitrade services a perfect solution.
Lee Contracting worked closely with OEM suppliers and the customer to plan and coordinate the best plan to receive, offload, uncrate, clean, and assemble two complete extrusion lines. The line consisted of two large presses (one 5500T and one 4000T) which required new foundation pits, with some areas having concrete 72″ thick, as well as utility trenching with trench covers that Lee Contracting’s weld/fabrication department fabricated in-house. There were also two material handling lines (which included quench systems, ovens, stretchers, and saws) that needed to be installed.
THE RESULTS
By utilizing Lee Contracting’s self-perform services, all aspects of the project were successfully completed before the due date. The project resulted in increased production capacity for the customer, which allowed the state-of-the-art facility to produce the highest quality product for the end user.
Subscribe and receive updates via email
Lee Contracting's challenge was to install a new two-inch air loop. This loop was to begin from the newly positioned air compressor room, extend up to the shop ceiling and surround the new work area.
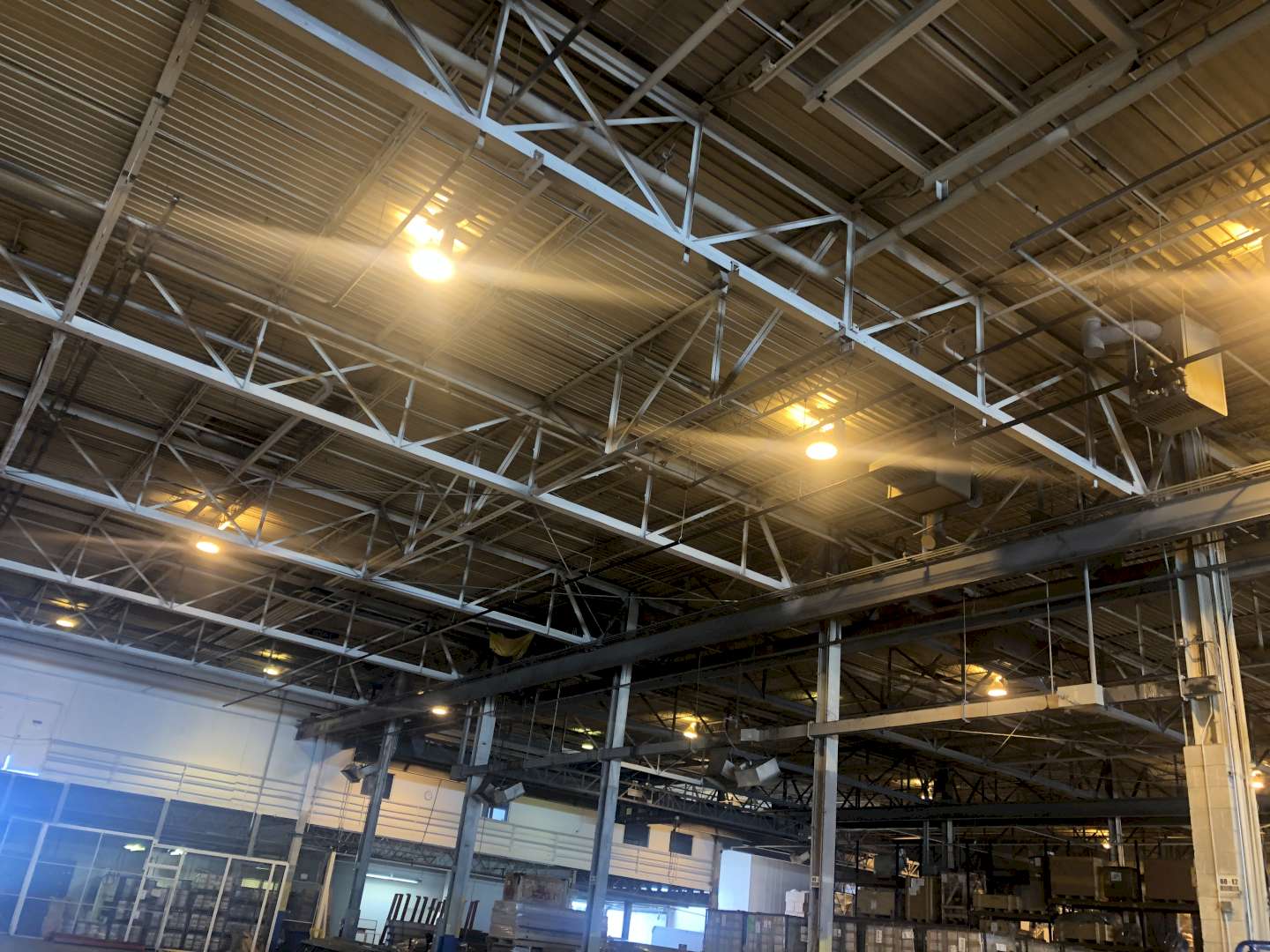
THE CHALLENGE
Adient, a manufacturer of automotive seating, operates on a global scale with a substantial base in Plymouth, Michigan. In a strategic move to enhance operational efficiency, Adient required a significant modification to their plant’s pneumatic system. The scope of this project involved the intricate task of installing piping to connect relocated air compressors with support equipment essential for production.
Lee Contracting’s challenge was to install a new two-inch air loop. This loop was to begin from the newly positioned air compressor room, extend up to the shop ceiling, and surround the new work area. Importantly, this new loop was also designed to serve as an extension of the existing tank, thus providing additional air storage critical for uninterrupted production processes.
THE RESULTS
Lee Industrial Contracting approached this project with a focus on minimizing disruption to Adient’s ongoing production. The installation was planned and executed in close collaboration with the customer to ensure production activities could continue without any interruptions throughout the duration of the project.
The Lee Contracting pipefitting team skillfully installed several water and air drops to the newly introduced D-line, enhancing the operational capabilities of the work area. Additionally, the compressor room was relocated and reworked to be more centrally positioned within the plant. This strategic relocation significantly optimized the functionality and accessibility of the pneumatic system.
Subscribe and receive updates via email
A large producer of long steel turned to Lee Industrial Contracting to upgrade multiple system components during their 30-day shutdown in June 2021.
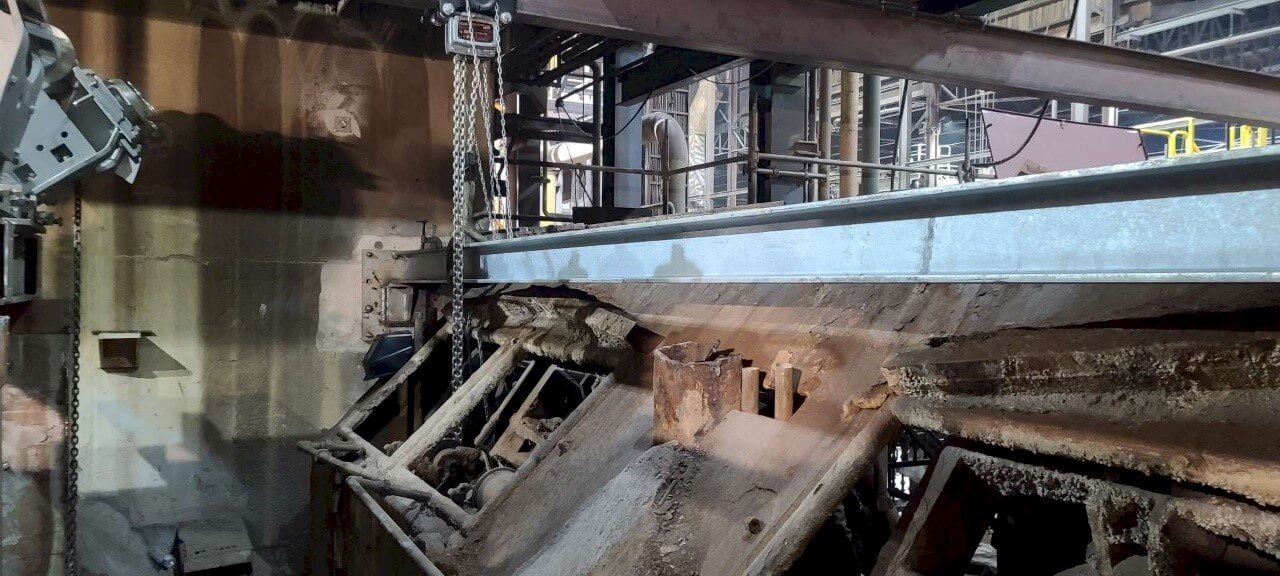
THE CHALLENGE
A large producer of long steel turned to Lee Industrial Contracting to perform several upgrades to their systems during a 30-day shutdown. Some of the notable projects during the shutdown included:
- Removal of an old cooling tower and reinstallation of a larger one. This allowed for better temperature control throughout the plant.
- Upgrades to stairways, structural steel and foundations.
- Upgrades to rolling mill saws, which involved removing the existing outdated equipment and replacing and reinstalling with new machinery.
- Assembly, installation and integration of a brand-new controls and material handling system on the client’s conveyors.
- Upgrading the plant’s cooling system.
- Removal of the client’s old caster spray chamber and the installation of a new one.
One major challenge the Lee Contracting team faced with this large-scale project took place during the removal and installation of the caster machine. Due to the location of the equipment in the plant, moving this large piece of machinery was nearly impossible without the quick thinking of Lee Contracting’s team to cut open the wall to safely remove the large piece of equipment. The teams then pre-assembled the new caster machine and rigged it through the same opening. After the machine was installed, Lee’s teams worked to weld the wall opening shut with galvanized steel plates.
THE RESULTS
Because Lee Contracting has all trades, equipment and tools in-house, they were able to meet the 30-day deadline. Not only did this save the customer time, but helped to get them back up-and-running by their deadline.