Department: Rigging
The line consisted of two large presses (one 5500T and one 4000T) which required new foundation pits, with some areas having concrete 72" thick, as well as utility trenching with trench covers.
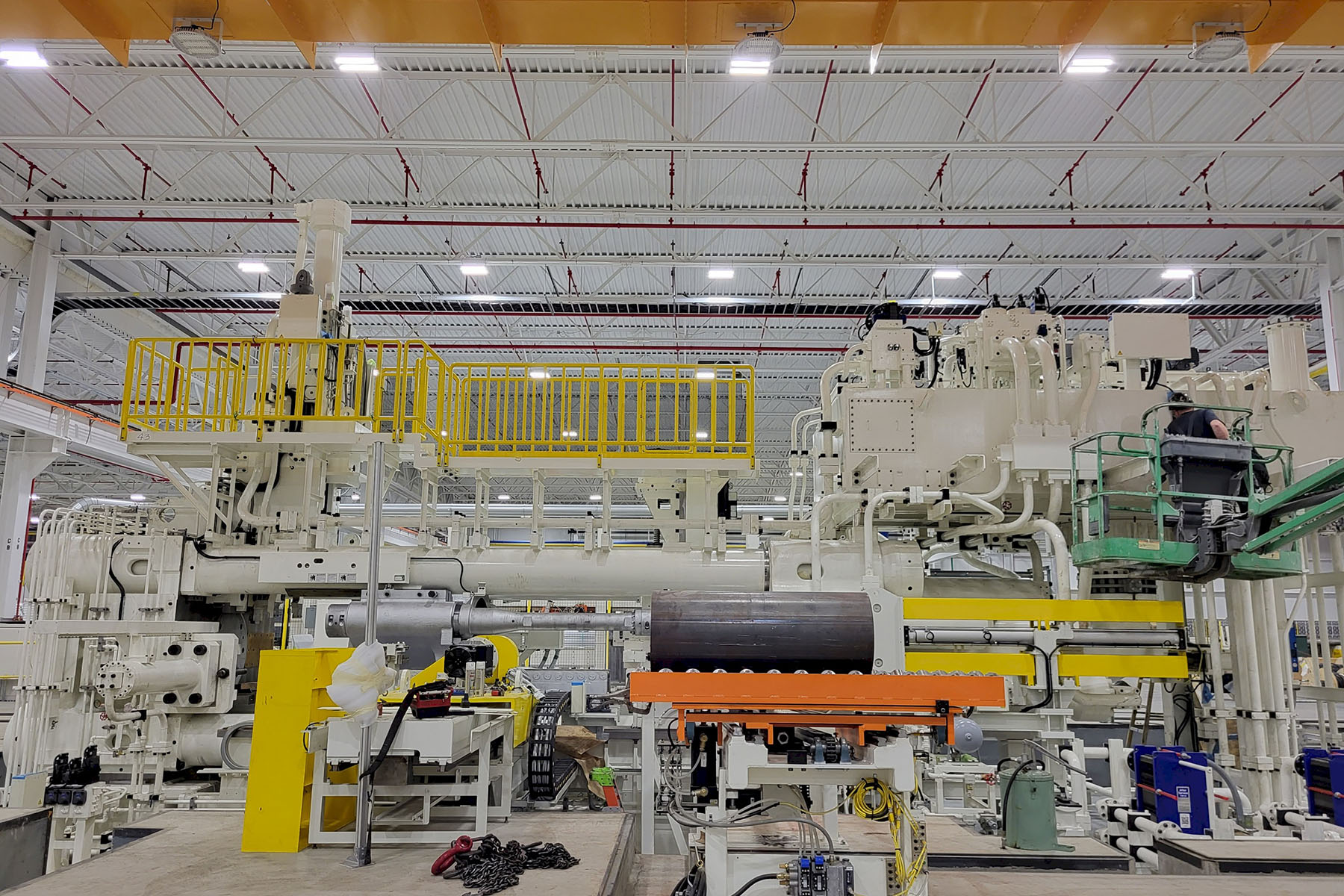
THE CHALLENGE
Shape Corporation needed additional manufacturing capacity within its extrusion facility. The timing and coordination needs of this project made Lee Contracting’s in-house, multitrade services a perfect solution.
Lee Contracting worked closely with OEM suppliers and the customer to plan and coordinate the best plan to receive, offload, uncrate, clean, and assemble two complete extrusion lines. The line consisted of two large presses (one 5500T and one 4000T) which required new foundation pits, with some areas having concrete 72″ thick, as well as utility trenching with trench covers that Lee Contracting’s weld/fabrication department fabricated in-house. There were also two material handling lines (which included quench systems, ovens, stretchers, and saws) that needed to be installed.
THE RESULTS
By utilizing Lee Contracting’s self-perform services, all aspects of the project were successfully completed before the due date. The project resulted in increased production capacity for the customer, which allowed the state-of-the-art facility to produce the highest quality product for the end user.
Subscribe and receive updates via email
Lee Contracting's challenge was to install a new two-inch air loop. This loop was to begin from the newly positioned air compressor room, extend up to the shop ceiling and surround the new work area.
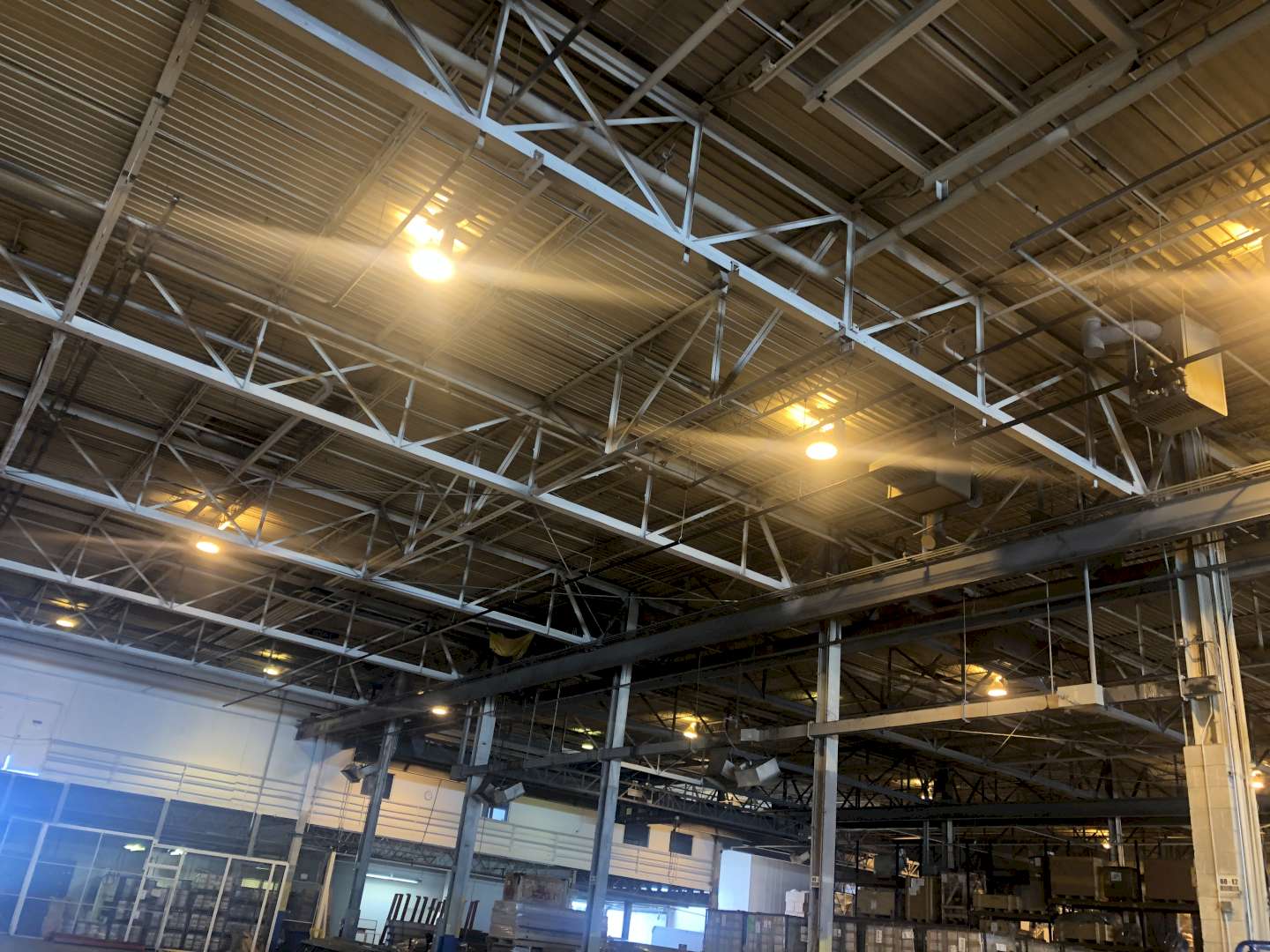
THE CHALLENGE
Adient, a manufacturer of automotive seating, operates on a global scale with a substantial base in Plymouth, Michigan. In a strategic move to enhance operational efficiency, Adient required a significant modification to their plant’s pneumatic system. The scope of this project involved the intricate task of installing piping to connect relocated air compressors with support equipment essential for production.
Lee Contracting’s challenge was to install a new two-inch air loop. This loop was to begin from the newly positioned air compressor room, extend up to the shop ceiling, and surround the new work area. Importantly, this new loop was also designed to serve as an extension of the existing tank, thus providing additional air storage critical for uninterrupted production processes.
THE RESULTS
Lee Industrial Contracting approached this project with a focus on minimizing disruption to Adient’s ongoing production. The installation was planned and executed in close collaboration with the customer to ensure production activities could continue without any interruptions throughout the duration of the project.
The Lee Contracting pipefitting team skillfully installed several water and air drops to the newly introduced D-line, enhancing the operational capabilities of the work area. Additionally, the compressor room was relocated and reworked to be more centrally positioned within the plant. This strategic relocation significantly optimized the functionality and accessibility of the pneumatic system.
Subscribe and receive updates via email
Remove and replace nearly 600, 90 pound interior cement kiln chains through a 26-inch manway in only 9 days? This is how we achieve the unthinkable.
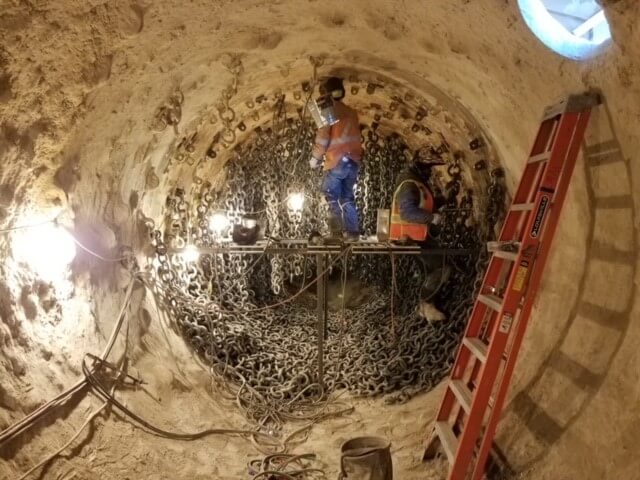
THE CHALLENGE
Lafarge Holcim, which specializes in cement, construction aggregates and concrete, operates two cement kilns out of their Paulding, Ohio location. Each kiln measures 800-feet long and 12-feet in diameter, and the inside contains over a thousand chains weighing over 90 pounds each.
Each chain is hung by tombstones welded into the steel walls of the kiln. When turned on, the chains slowly rotate, crushing the mined rock, which is then heated to 1,500 degrees Celsius and continues to rotate until the rocks are crushed into fine dust.
Over time, the chains on the interior of the kilns become worn and need to be replaced. Lafarge Holcim contacted Lee Contracting to remove and replace nearly 600 chains in a nine-day window – which is no small feat. The kilns had uneven flooring, the chains created a trip hazard, limited space, no lighting and the dusty conditions.
THE RESULTS
To remove the heavy chains from the cement kiln, Lee Contracting’s teams attached them to a crane and raised the chains through a 26-inch manway on the side of the kiln. The team was also tasked with removing any worn tombstones and welding new ones in place in a precise pattern. The Lee Contracting rigging team then lowered new chains into the kiln, which were reattached to the tombstones.
At the end of the project, the client was pleased with the crew’s teamwork and for Lee providing a cost-effective and timely solution for this project.
Subscribe and receive updates via email
The crown of an automotive supplier’s Verson press machine was damaged beyond repair. Installing a new one on their existing press was a…crowning achievement.
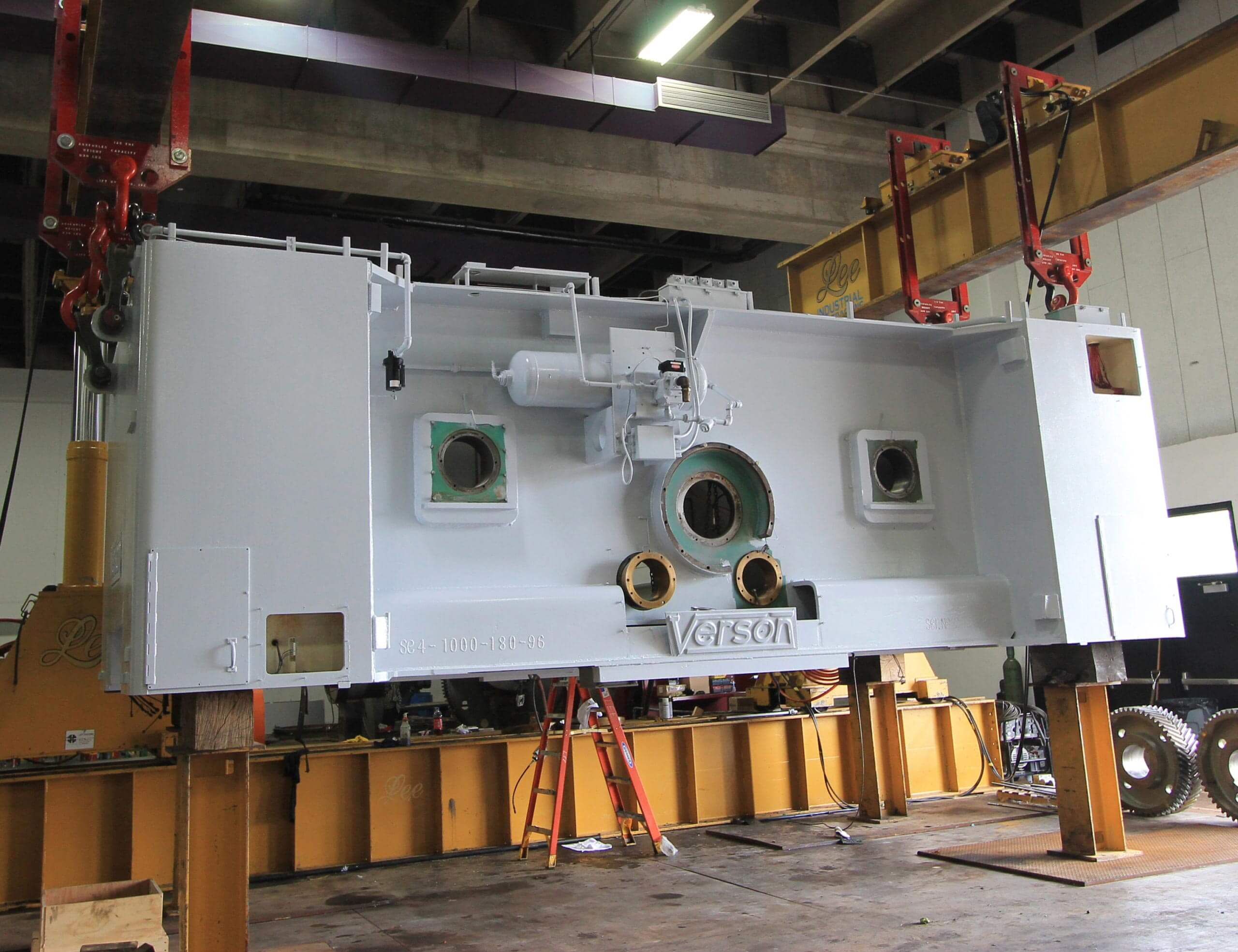
THE CHALLENGE
After the crown of one of the largest tier one supplier’s Verson press machine became damaged beyond repair, the company purchased a new one and called Lee Contracting to install the crown on their existing press. However, the job consisted of much more than simply removing the old crown and setting the new one. The rigging team first went to the site to pick up the old crown with their in-house gantry system, rolled it over and set it down on bunks. Next, the Lee Contracting maintenance and repair team disassembled the old crown in hopes of using those same parts in the newly purchased one.
While the crown was disassembled, the Lee Contracting team found damage to the eccentric bushings. This is where Lee Contracting was presented with the first challenge. Eccentric bushings help to reduce friction between two objects and are critical because of their ability to minimize vibration and noise. Ordering new bushings could take six to 10 weeks for delivery, but Lee Contracting knew that would push the project timeline back significantly.
THE RESULTS
A two-week turnaround for the client instead of six to 10 weeks.
Once the crown was disassembled by the maintenance and repair team, the rigging team hauled the old crown out and brought in the new one. Thankfully, the team used their experience, and positive supplier relationships, to think outside of the box. Lee Contracting was able to get unfinished bushings from the supplier, machined them and hand grooved each one to spec in-house.
During the project, the Lee Contracting maintenance and repair team also:
- Re-built the hydraulic overload protection system to prevent any damage to the press in the event of an overload
- Fixed damaged intermediate gears by in-house welding the entire shaft
- Put the machine back together with the newly refined parts
Subscribe and receive updates via email
When a heavy industry client in Indiana needed a Steel Slitter Line installed, Lee Industrial Contracting was called to put their “turn-key solutions” tagline to good use.
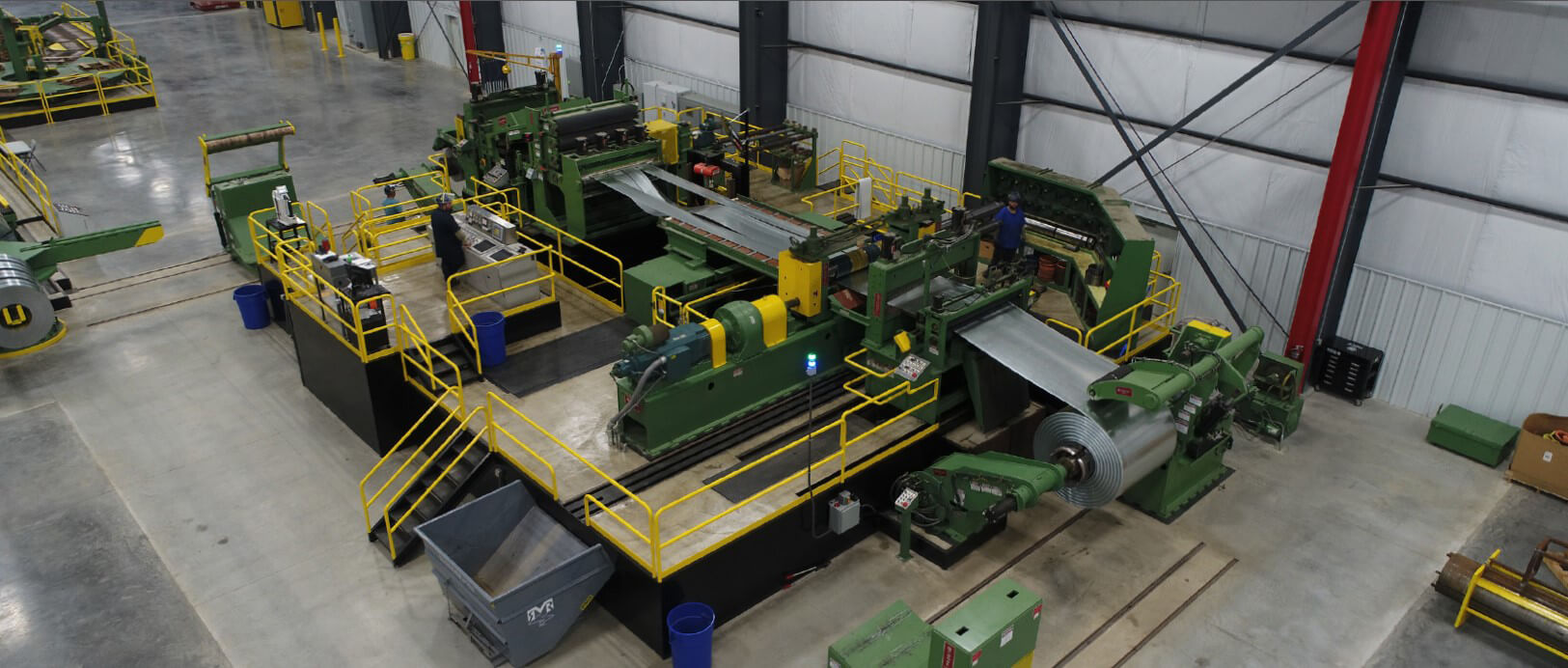
THE CHALLENGE
When a heavy industry client in Indiana needed a steel slitting line installed, they called on Lee Industrial Contracting’s Power of One. Lee Contracting needed to construct new foundations for the machinery, while the building remained partially open.
Since the project was taking place in the middle of winter, the Lee Contracting team had to take extra measures to ensure the project was done safely and without delays.
THE RESULTS
To minimize disruption to the customer, Lee Contracting installed installed temporary walls with panel doors to keep in the heat and to allow access for construction equipment and concrete trucks. This allowed Lee Contracting’s team to easily excavate, install underfloor conduits and set reinforcement steel.
Next, Lee Contracting’s in-house fabrication department constructed and installed embedded structural steel beams, entry and exit turnstile anchor bolt frames, coil car rails with support channels, utility trenches with cover plates, as well as stairs and handrails.
Once the foundations were finished and the concrete cured, Lee Contracting’s rigging crew offloaded, set in place, aligned, leveled and anchored the new equipment onto the new foundations.
Following the installation of the equipment, the Lee Contracting electrical team installed new wiring, from the equipment to the main control cabinet.
Subscribe and receive updates via email
Designing and pouring foundations for 8 large milling machines is a pretty straightforward project. Doing it on frozen ground while buildings are being constructed around it took Lee’s Power of One.
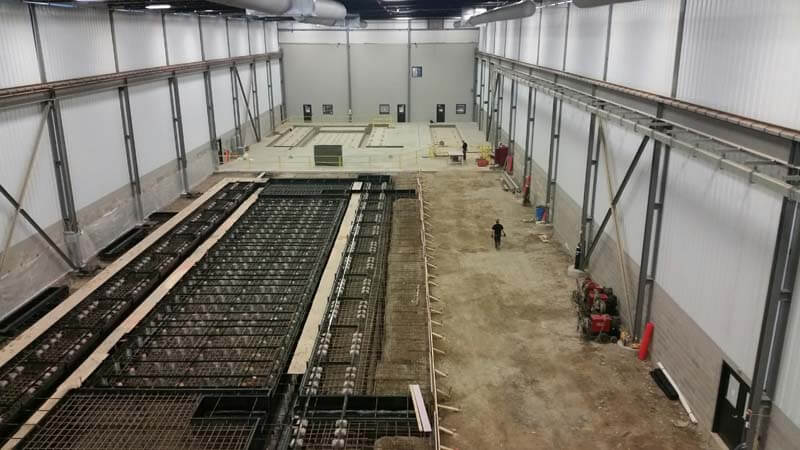
THE CHALLENGE
Visioneering, a leading aerospace designer, manufacturer and installer of assembly systems for the aerospace, defense and space industries, began building a new facility with a goal of consolidating their buildings and machinery under one roof. They contacted Lee Industrial Contracting to perform a design/build project, which included pouring foundations for eight large milling machines during the development of the new facility.
It was essential to begin planning with the Visioneering facilities team to ensure the layout resulted in a good process flow. Because these new foundations would be poured while the new facility was under construction, the Lee Contracting team had to plan around various timelines and other work being done at the site.
THE RESULTS
To meet the project timeline of the customer, Lee Contracting had between eight and 12 workers on the site at any one time during this year long project. As a testament of the Lee Contracting team’s experience, they were able to complete the machinery foundations in under 10 months, exceeding timeline expectations.
After the foundations were finished, Lee Contracting transported and installed the machinery in the new location. The foundations were completed with such precision that there were no problems installing the eight milling machines.
Due to Lee Contracting’s quality work, ability to offer multiple trades under one roof and the company’s skill of completing projects ahead of schedule, the team has returned to the Visioneering facility to complete a variety of other projects.