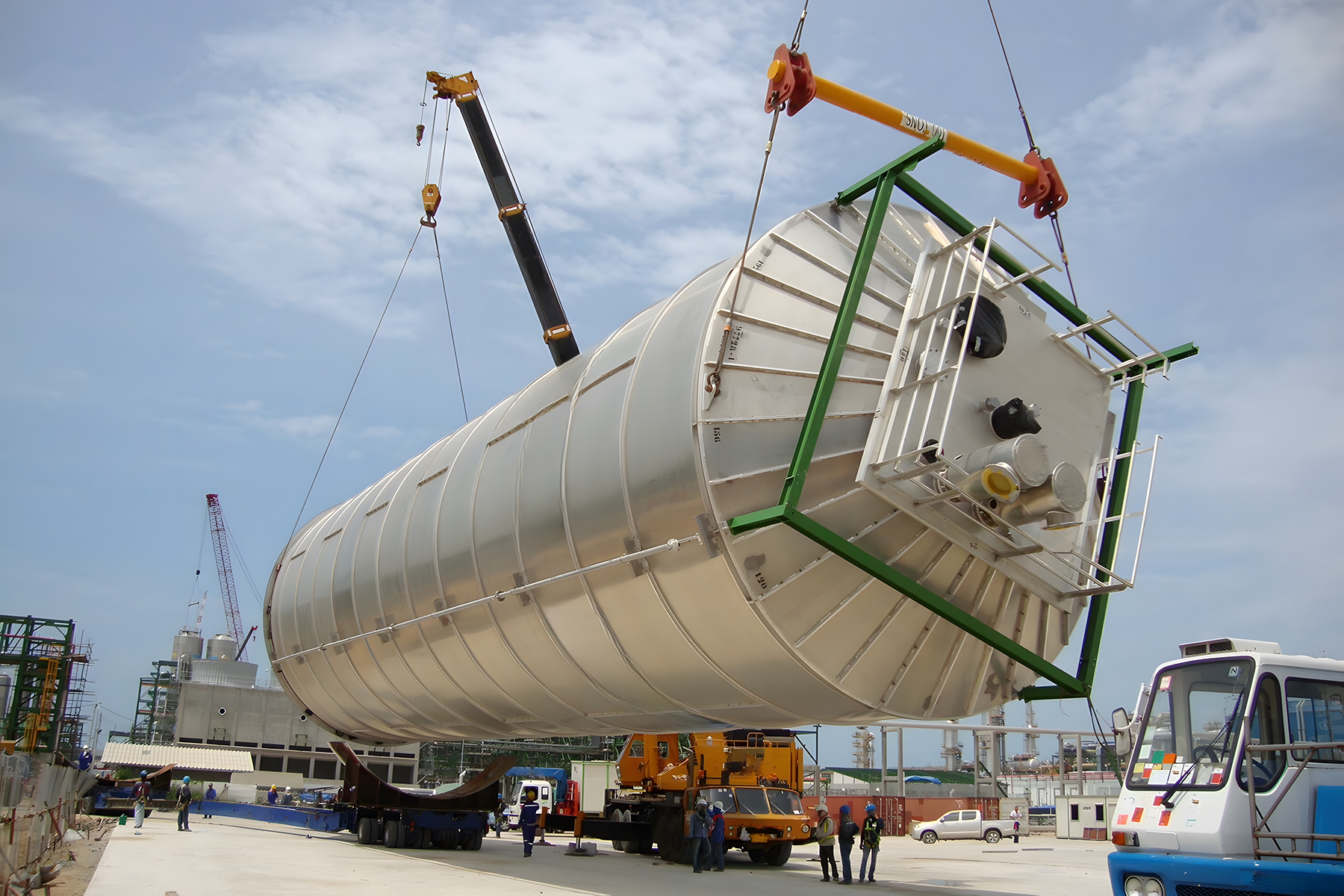
It was supposed to be a simple move – relocating a large piece of equipment to another part of the facility was projected to take just a few days. But once the project started, problems began piling up.
The industrial rigging contractor finished their part, but the electrical team wasn’t scheduled for another three days. Then, a crucial support bracket turned out to be the wrong size and the company had to wait a full week for an outside industrial fabricator to make a replacement.
What was meant to be a short disruption stretched into nearly a month of downtime, putting production behind schedule and causing frustration at every level of the business.
If this scenario sounds familiar, you’re not alone. This type of situation plays out all too often in industrial relocations, and the main issue is this: too many industrial contractors and too many moving parts, all operating on their own timelines.
The key to avoiding these delays? A single-source, turn-key approach.
The Power of One: An In-House, Turn-Key Solution
When it comes to industrial projects, coordinating multiple vendors and the headaches it brings can drag out timelines and lead to more downtime. But if you work with an industrial contractor that can handle every aspect of the project in-house without needing to subcontract, like Lee Contracting, you can dramatically shrink timelines and downtime.
So instead of juggling separate contractors for rigging, electrical, mechanical, and fabrication, you get a fully integrated team that works together from start to finish. This means:
- One project manager overseeing the entire process.
- No delays waiting on subcontractors.
- The ability to adapt in real-time to challenges.
Lee Contracting’s “Power of One” approach ensures that machinery relocations happen as efficiently as possible, minimizing downtime so you can get back to normal operations quickly.
How Lee Contracting Gets the Job Done Faster
When it comes to equipment transfers, the ability to move quickly is everything. Downtime means lost revenue, and every delay adds up. That’s why in-house teams and resources make a critical difference.
Here are just a few advantages that The Power of One brings:
- Rigging Without the Wait: Because Lee has its own heavy-lift equipment and employs full-time rigging specialists, projects don’t get stalled waiting on availability from an outside contractor. If something needs to be moved, we can deploy rigging teams immediately.
- On-the-Spot Fabrication: Unexpected issues during a project often turn up, including missing or incorrect parts. Instead of waiting days or weeks for an external fabricator to deliver a solution, an in-house fabrication team can custom-make the needed part on demand, keeping the project moving.
- Immediate Installation: Because the electrical and mechanical teams are part of the same company as the rigging crew, installation can begin as soon as relocation is complete with no lag time between phases.
This integrated approach means that what could take weeks with multiple contractors can often be completed in days, saving your company time and money.
How a Turn-Key Approach Contributes to Long-Term Success
A turn-key approach delivers benefits far beyond just the one move. When you work with a team that handles everything in-house, you’re not just getting a one-time solution, you’re building a partnership.
This means the next time you need to expand or reconfigure your plant, you won’t have to start from scratch. You’ll have a team that already understands your facility, your equipment, and your operational goals, so every future project goes faster and smoother.
Equipment relocation doesn’t have to mean weeks of downtime. By tapping into Lee Contracting’s Power of One, you can complete a major equipment relocation as quickly as possible so you can avoid extended downtime and keep production on track.
Need to relocate industrial equipment? Request a quote from our team today.