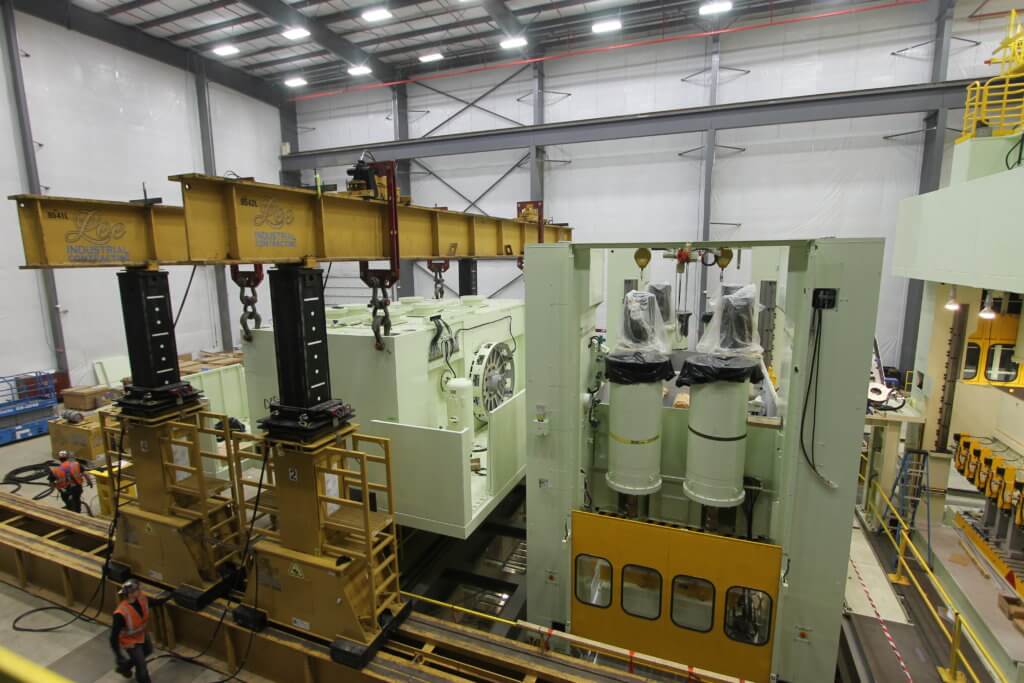
For the last 30 years, Lee Industrial Contracting has exceeded customer expectations in the aerospace, automotive, energy, environmental and heavy industries. We have proven our ability to anticipate industry trends and respond with ground-breaking recommendations. The scope and challenges of our automotive projects have allowed us to exhibit our team’s ability to design innovative solutions to solve the toughest problems for our customers.
Dyno Installations
Challenge: Locate a dyno lab in the middle of a production floor with minimal disruption to productivity.
Our customer needed an innovator with the experience to create a dyno lab within their production facility, so they naturally called Lee Industrial. In collaboration with the building, electrical, fabrication, foundations, mechanical, paint and rigging departments, our team installed the dyno lab inside the existing structure. We enabled the lab to house two separate pieces of equipment with different functionality by upgrading the power and installing a new cooling loop. To upgrade the power, we orchestrated strategically planned outages for facility downtime to minimize production impacts while upgrading their power capabilities. Our hardworking team then coordinated the installation of the dyno and bedplate to ensure that the project was completed within scope, time and budget with the highest quality.
International Press Relocation
Challenge: Coordinate the international relocation of 13 presses ranging from 200 to 4000 tons each from St. Catharines Ontario, Canada to Pontiac, MI.
When our client needed their high-tonnage equipment refurbished, it presented a unique problem. With a tight timeline to complete the restoration, they needed experienced professionals that could not only renovate the machinery but coordinate the transportation and handle the border requirements. The client contacted Lee Industrial for a solution. Working with the building, fabrication, foundations, maintenance and repair, mechanical, paint, rigging and transportation departments, we shipped the 60-year-old presses via rail to our Michigan location where they were fully refurbished to like-new condition. We then transported them to their final destination for installation, meeting the deadline.
Mill Line Installations
Challenge: Install 17 mill lines, containing three to six pieces of equipment each, within a short timeline.
With commitments looming for automobile manufacturers, our client required the rapid, precision installation of multiple mill lines with high-tech equipment. Each of the 17 mill lines contained one to three robots and two to three mills. With careful coordination and focus on quality, efficiency and expediency, we installed utilities for the electrical and mechanical lines. We successfully shaved a week off the line installation timeline, delivering the customers solution in time to meet their production commitments.
Press and Feed System Relocation
Challenge: Install a new press in the middle of an existing production area by raising the roof to accomodate it.
At Lee Industrial, we are proud of our reputation as the provider of innovative solutions involving plant relocation, machinery moving and plant restructuring, as well as our past successes with our client projects. It is that reputation and successful track record that led our customer to contact us for another solution. After acquiring a new press, our client discovered that their facility would not accomodate the new equipment as it was too tall. The solution they sought was to have the roof raised so that we could install the new press.
Working with the building, electrical, fabrication, foundations, mechanical, paint and rigging departments, our team created a foundation pit for the press and feed system. We then moved the press and feed system from another city to the client site. After raising the roof, we disconnected, relocated and reconnected the electrical panel and electrical and piping utilities. By providing a temporary safety barrier, we enabled production to continue uninterrupted throughout the project that was executed by the expected deadline.