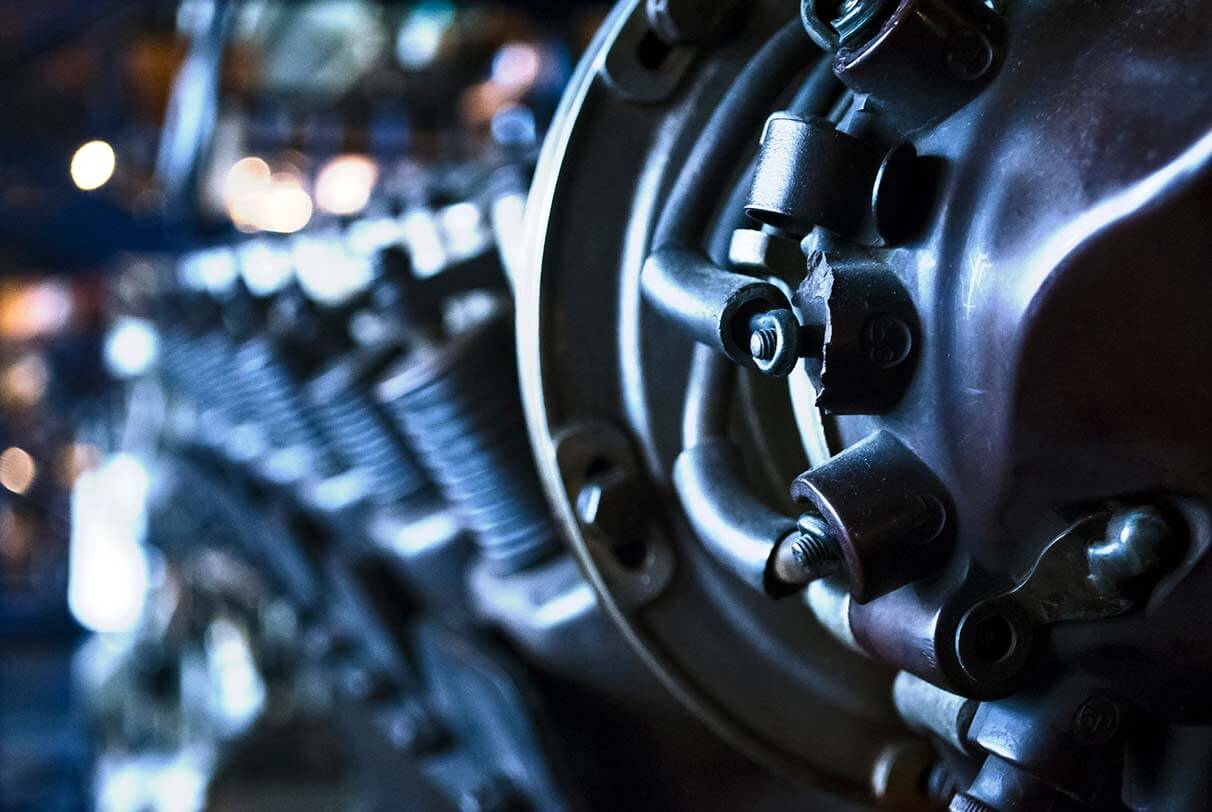
From its humble beginnings in a small Dayton, Ohio, bicycle shop 100 years ago to landing a man on the moon to creating materials that affect almost every aspect of daily life, the aerospace industry is a worldwide leader in product and manufacturing innovation. As an industry that utilizes advanced equipment and technologies, aerospace contractors face many different challenges from those found in other industries.
New materials, such as composites and lightweight aluminum alloys, are slowly shifting aerospace manufacturing to increased automation, but manual processes still hold a strong foothold. As in any industry, automation does not remove the need for effective maintenance strategies. In fact, with the extreme filtration, lubrication and other tolerances required in aerospace production, diligent maintenance becomes even more important in reducing equipment downtime.
Predictive and proactive are key
A study by GE Digital found that 70 percent of respondents didn’t have a firm handle on when equipment maintenance, upgrades or replacements were needed. And only 24 percent use data and analytics for predictive maintenance. There is clearly room for improvement.
Predictive maintenance focuses on reducing unnecessary upkeep and avoiding unplanned downtime and equipment failures. The process looks at historic data analysis, equipment inspections, operator input and sensor data to drive proactive equipment and systems servicing.
These activities help determine when equipment should be serviced and can spot developing problems before they result in unplanned downtime or outright equipment failures. Predictive maintenance is more efficient than scheduling maintenance based on time considerations alone, because servicing can be performed on an as-needed basis.
Set maintenance KPIs
Unplanned equipment downtime can cost thousands of dollars per day. Monitoring equipment uptime and comparing to historic data are important aspects of reducing these kinds of occurrences. Clearly-defined performance targets will help focus attention on what needs to be monitored and analyzed. Here’s a list of suggested indicators:
- Mean Time Between Failures tracking can guide preventative maintenance interventions.
- Mean Time To Repair looks at required repair downtime to analyze your response time to resolving breakdowns.
- Overall Equipment Effectiveness measures asset effectiveness based on availability, performance and quality.
- Cost of Asset Maintenance can guide effective budget planning. Discrepancies that show here can inform your preventative maintenance plan.
- Cost to Replace vs. Cost to Repair can help determine the cost effectiveness of replacing an asset instead of pouring time and money into repair.
- Unplanned Maintenance Percentage is a good test of your preventative maintenance plan’s effectiveness. Shoot for a ratio of 10-20 percent unplanned to 80-90 percent planned.
- Work Order Resolution Time is a good marker for how well your maintenance teams are performing. A strong preventative maintenance plan can lower the number of work orders and reduce backlog.
Environmental monitoring is also critical for aerospace contractors. Many of the advanced materials used require strict adherence to temperature, humidity and other environmental standards, and ensuring those requirements are met should be factored into all maintenance considerations.
Get to know the OEM
Maintaining new or complex production equipment should start with a risk assessment that includes the asset’s maintenance plan. You want to know everything there is to know, and the best place to find that is from the manufacturer. While larger aerospace companies often have maintenance performed by the manufacturer, there is a wealth of maintenance information useful to industrial contracting services to be found in equipment manuals and discussions with the manufacturer’s personnel.
Train, train, train
Any maintenance plan is only as good as the people doing the work. So it only makes sense for aerospace contractors to equip the best people with the best possible training. This is especially important when dealing with new technologies that often require new skillsets. Relying heavily on OEM information will help ensure training prepares personnel to provide effective and efficient maintenance services.
Recent changes and challenges in manufacturing have seen a loss of maintenance technicians to other fields and many companies have scaled back the number of technicians on staff. Industrial contracting services that offer both planned and reactive maintenance services can help fill the void caused by these losses.