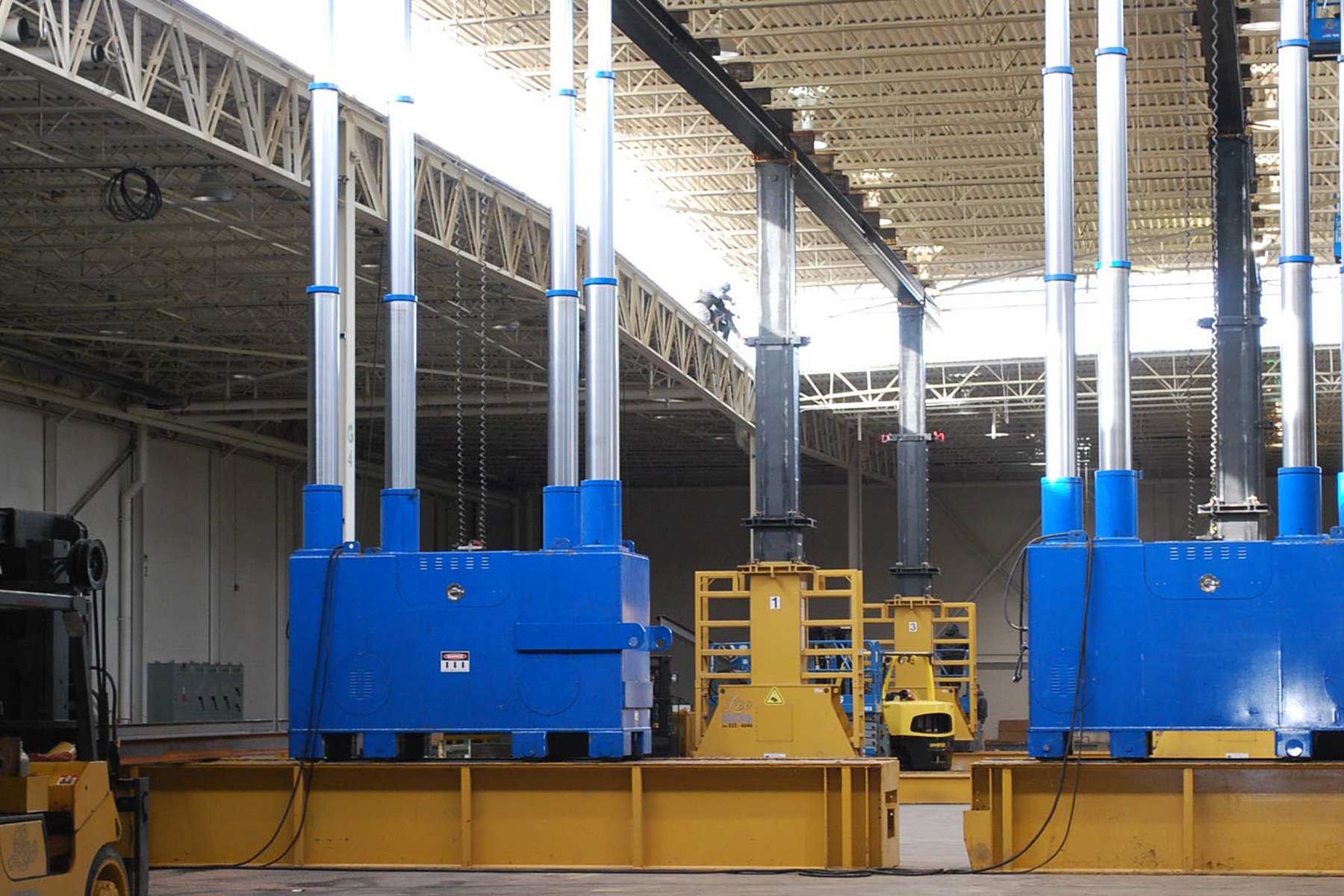
As your business and industries evolve, renovating your industrial facility will be necessary at some point. This is actually a significant milestone – it signals that your company has stood the test of time and is ready for improvements that boost efficiency, safety and productivity.
While a renovation is an exciting step toward improving and optimizing your facility, it does come with its challenges while going through it. In particular, how do you make major changes to your space without affecting day-to-day operations? Even minor disruptions can lead to costly downtime, so strategic planning is essential.
We’ve put together a guide to industrial facility renovation planning so you can keep production running smoothly while making necessary upgrades. By following this guide – and working with an experienced industrial contractor – you can minimize disruptions while ensuring a successful renovation project.
1. Assess the Scope and Impact
As with nearly any industrial project, proper planning is an essential first step that can make a huge difference to ensure the entire project goes smoothly. Before starting any renovation, you must first evaluate exactly how the project will affect daily operations.
Before beginning your renovation, be sure to conduct a thorough site assessment to identify the areas that need work and how construction might interfere with your systems. What are the high-priority zones that must remain operational? What might pose a potential risk – such as disruptions to power, HVAC, or safety systems?
A detailed impact analysis helps create a renovation plan that allows you to anticipate and prepare for any hiccups, helping to keep downtime to a minimum.
2. Go with a Phased Approach
One of the best ways to maintain operations during renovations is by breaking the project into manageable phases. Prioritize upgrades that have the least impact on workflow and schedule major work during off-peak hours or planned downtime.
For example, if you know that spring is your busy season but summer is typically slower, you can schedule less disruptive renovation work during peak times and save the more demanding upgrades for when you know production will be slow.
A well-structured timeline goes a long way in making sure no critical areas are compromised so your team can continue production while renovations move forward.
3. Consider Temporary Solutions
To maintain productivity, consider implementing temporary solutions that allow your industrial facility to function while work is underway.
This could include setting up temporary workspaces, rerouting operations or using modular construction to minimize on-site disruptions. Prefabricated components can also help speed up installation, reducing the time needed for on-site work.
A skilled industrial contracting partner should be able to construct these areas so your team can continue performing their core jobs.
4. Leverage Technology
Incorporating technology into the planning process can help anticipate challenges and streamline renovations. Creating digital twins and 3D modeling helps facility managers and industrial contractors visualize the entire renovation process before it begins, so they can identify potential conflicts in advance.
By simulating real-world conditions in a virtual environment, digital twins and 3D models allow teams to test different renovation scenarios, optimize workflows and foresee potential bottlenecks. Additionally, these tools can be used to map out temporary workarounds, such as rerouting foot traffic or repositioning equipment, to maintain productivity throughout the project.
5. Maintain Safety and Compliance Throughout
Nothing derails operations like an accident or injury. During any renovation, safety must be a top priority, especially when new work is happening alongside rote operations.
Clear safety protocols should be drawn up and implemented to protect both employees and contractors. Compliance with OSHA and industry regulations is essential, and regular safety inspections should be conducted to ensure a secure work environment.
Be sure to educate and communicate with your employees to make sure they understand potential hazards and how to deploy the appropriate safety measures.
6. Select the Right Industrial Contracting Partner
One of the most important decisions you can make is choosing an industrial contractor with experience conducting renovations while your operations continue. Look for a partner with experience working in active industrial environments and offers a full range of services – including design, engineering, fabrication, rigging, electrical and mechanical contracting.
Pro tip: Be sure to involve your industrial contracting partner as early as possible in the process. An experienced partner has performed facility renovations numerous times and can propose creative solutions you may not have considered.
A contractor who has fully in-house teams and doesn’t rely on subcontractors provides better control of project timelines, quality and communication. A strong relationship with an experienced industrial contracting company, like Lee Contracting, ensures that work is completed efficiently with minimal disruption to your operations.
Contact us today to discuss how we can support your next renovation project.