Relocating heavy equipment, such as a stamping press, is an important decision for many manufacturing facilities. Whether equipment is being moved from one side of the facility to another, or across the country, there are many factors to take into account when planning to relocate equipment.
You probably already know that the equipment dimensions are important to the move, but there are several other measurements that need to be considered to ensure a successful move. These include:
- Door Size
- Floor rating
- Obstacles
- Open Access
- Weights & Dimensions
Planning the transportation of your press is a critical step. The weights and dimensions of the equipment and its components are essential when it comes to estimating transportation costs. The best way to find the weights of the components is from the original equipment manufacturer.
Most large machinery exceeds the weight capacity of a standard five-axle tractor/ trailer combination. Oftentimes, when transporting heavy equipment, higher-capacity transport equipment must be specified, routes must be established, and special permits must be obtained. Depending on the state, some permits may take four to six months to obtain.
When planning transportation, you should also take into consideration the destination of the equipment. The destination will help to determine which transportation equipment is needed, which permits are required and the preparation and packaging requirements. Some states have different requirements for overweight and over-dimensional loads, so it is imperative to find equipment that can meet the requirement of all states through which the loads must travel.
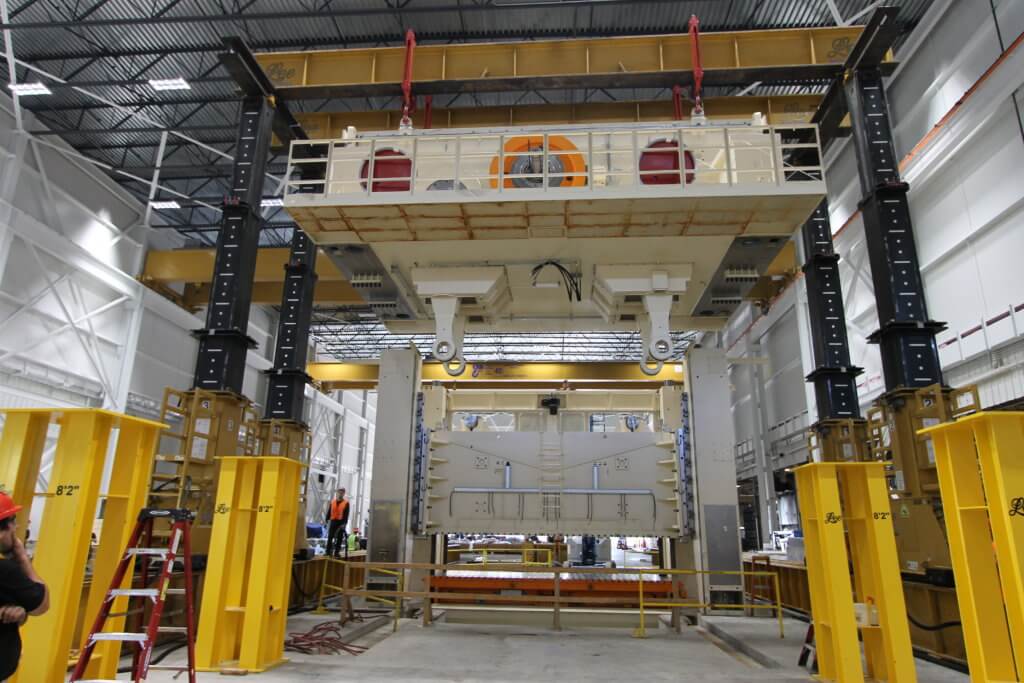
Installation
The last step in ensuring you have a successful press move is the installation of the press. Hiring the right riggers can make a world of difference during the installation process. The right rigging company will have the proper equipment for the job, including cranes, gantries, fork trucks and man lifts.
The equipment’s new location will have its own set of challenges compared to its previous location. These might include:
- There might not be a pit or foundation installed for the equipment.
- Lower ceiling heights, which requires the riggers to use special assembly procedures.
- The doorways might not be large enough which would require the machinery to be either disassembled or for the doorway to be made larger.
- Power supplies to the building might not be large enough to handle the new equipment.
- Air compressors might not be large enough to handle the new requirements.
At Lee Contracting, we can solve all these challenges with our 13 in-house capabilities working together. Our turn-key solutions process takes the time to ensure that every aspect of your project is carefully planned and executed with perfection.
We work with you to complete your project safely and efficiently. Lee Contracting has over 30 years’ experience and a full team of experts, who have the capabilities to complete all your required services as a single-source contractor throughout the United States.
Call us today to receive your free quote (888) 833-8776 or visit our website.