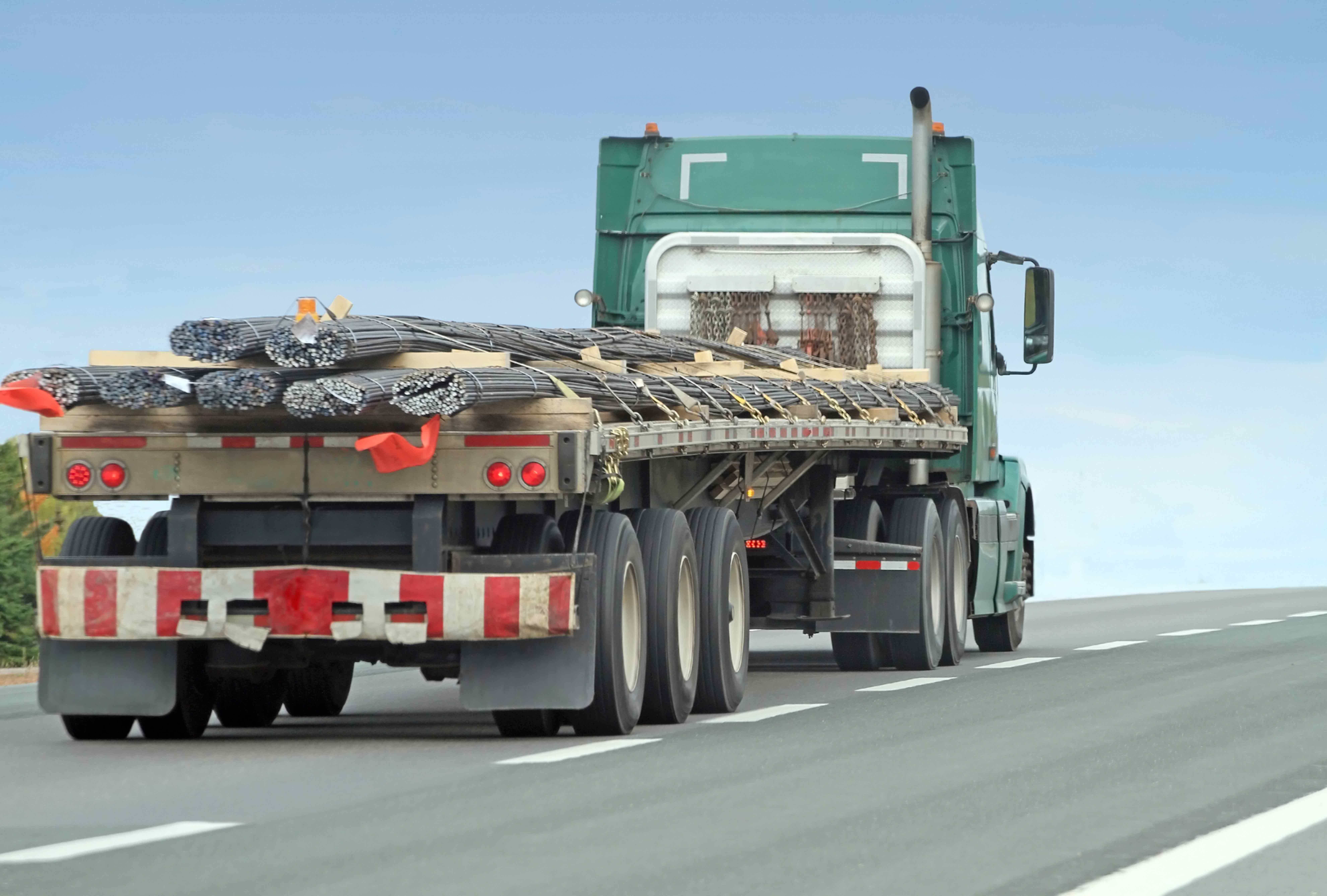
Shutdowns. Layoffs. Plant closures. Projects on-hold. And now, shortage-driven price inflation. The global pandemic has thrown the entire world into chaos.
In the industrial contracting space, the most noticeable problem in recent months has been price and supply volatility in materials. According to the U.S. Chamber of Commerce, 84% of contractors face at least one material shortage. And for 46% of industrial contractors, material shortages are having a high impact on projects.
A Perfect Storm
When the pandemic took hold in 2020, shutdowns across the board brought the nation, the economy and our industry to a near standstill. Almost overnight, many industrial contracting projects were put on hold, although work did continue in regions of the country where construction was considered an essential industry. Those projects that did move forward faced extended lead times and often severe restrictions on how work was performed.
From the start, manufacturers began shutting down operations. This quickly led to shortages of materials for construction. The effects were highlighted in steel production, as mills were closed around the world.
With the easing of restrictions, buyers have seen the basic law of supply and demand showcased, in that as demand for materials exceeds supply, prices rise accordingly. In industrial construction, demand is still running ahead of supply, fueled by owners who are scrambling to restart projects that had been put on hold. Additionally, companies are also moving rapidly to get new projects underway.
Even with the challenges, the construction industry has been somewhat less affected than many others. Many industrial contractors are experiencing high workloads, both in backlogged work from 2020 and projects whose timelines have been accelerated.
A New Normal?
The short-term situation has seen major changes in the way projects unfold, especially in the bidding process. Because of pricing volatility, the old norm of 30-60-90 day quotes has been replaced by quoted prices that are now only good until the end of the day due to the rapidity of price changes. The effects are felt on both the owner and contractor side, introducing a level of uncertainty not seen before in heavy industrial construction.
Project owners and industrial contractors don’t expect the situation to ease for at least another year. And even as supplies slowly become more available, labor shortages continue to delay projects. For example, it’s not unusual for loaded trucks to sit for weeks before delivery, due to a lack of drivers. At least in the short term, price and supply volatility are expected to be the norm.
The appearance of the Delta variant has once again put the nation on edge. Its effects on the reopening of the U.S. economy are, of course, currently unknown. But even if the variant should have a significant impact, the effects are not expected to be as severe as those of the original pandemic, because industrial contractors and suppliers have learned how to operate effectively under adverse conditions.
A Light in the Tunnel
As industrial contractors closely monitor the ever-changing construction landscape, supply challenges are being addressed by aggressive increases in materials inventories. Leading firms with solid relationships with suppliers and strong buying power are maintaining higher inventory levels and working with stakeholders to keep them up to date on supply and price issues.
This is a boon for project owners, who can benefit from partners that have seen the writing on the wall and made significant inventory investments. Contractors who are unable or unwilling to risk increasing their materials inventory will likely be less competitive going forward.
In addition to our massive in-house inventory, Lee Contracting has a dedicated team of buyers scouring the world for the best combinations of price and supply, ensuring we have the inventory available now to complete your project without delay. Contact us today to discuss the benefits to your next project.